We’re starting with molecular design and 3D microprinting research today, before moving on to a robotic 3D printer partnership. Then it’s on to a variety of applications, including a 3D printed concrete bridge, 3D printed furniture, 3D printed shoe soles, and finally 3D printed prosthetic sockets.
Researchers Use Molecular Design for Additive 3D Microprinting
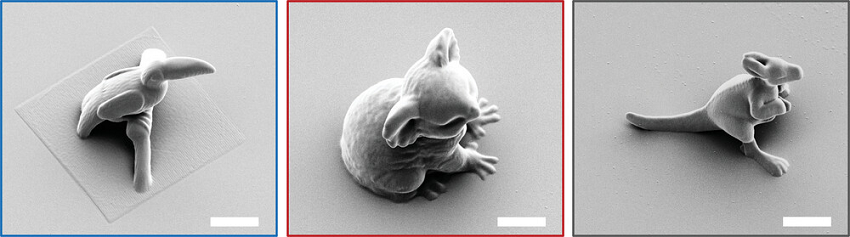
Representative SEM images of 3D microstructures printed with 2PLP with alternating (blue), triblock (red), and block (gray) oligomer inks printed with 0.25 wt.% DETC demonstrating versatility of the oligomers as inks for 3D microprinting. Scale = 10 µm. (Reprinted with permission from Wiley-VCH Verlag)
You can find macromolecules with complex, defined structures in nature, but not often in synthetic macromolecules. Sequence-defined approaches enable more precise control of the macromolecular structure, but other than niche sectors like data encryption, there aren’t many applications. But, a team of researchers from Heidelberg University and the Max Planck Institute for Medical Research used rational molecular design to direct sequence-defined materials as 3D printable inks. By combining two-photon laser printing (2PLP) at the microscale with sequence-defined macromolecules, they could program print resolution, mechanics, and fabrication limits to develop precise, intricately structured materials.
The researchers formulated three inks by synthesizing oligomers, and used them to 3D print very intricate “buckyball” structures. Using sequence-based control to dictate the print behaviors, the team then microprinted intricate plants, mammals, and birds. By “manipulating the positioning of photocrosslinkable units along an oligomer backbone,” they were able to program major differences in the topology, print resolution, mechanics, and fabrication windows of the microscale prints. This ability to use sequence design to tailor 3D printable inks has many potential applications for constructing specialized devices, such as targeted drug delivery vehicles, lab-on-a-chip and bio-integrated electronics, labeled cell growth scaffolding, and even molecular circuit components. You can learn more about their work in their published paper.
TGS Offering Flexbot Research XL for Czech Republic Customers
Dutch company CEAD, a pioneer in robotic large format additive manufacturing (LFAM) solutions, announced a partnership with advanced engineering firm TGS, located in Mýto, Czech Republic. At an open house in December, TGS launched its new Flexbot Research XL platform, which the CEAD team had installed in September. Attendees got to see live demonstrations of the Flexbot Research XL, printing with Airtech Advanced Materials Group’s Dahltram T-100GF fiberglass composite that’s reinforced with recycled-grade co-polyester resin. With a print volume of up to 3 x 1 x 2.5 meters and a versatile range of composite materials—including PEEK and glass- or fiber-reinforced—the novel large-format printer will allow TGS to offer 3D printing services to its customers in the Czech Republic. Additionally, TGS will also serve as a reseller for CEAD’s Flexbot and extruders in the country and other nearby regions.
“The open day event highlighted once again the importance of the strategic partnership between CEAD and TGS. This synergy will leverage our competencies to support customers in the implementation journey for large-format additive manufacturing solutions in Czeck and Slovakia markets,” said Andrea Baldolini, sales team lead at CEAD.
Holcim Unveils Circular 3D Printed Concrete Bridge
Sustainable building solutions leader Holcim launched a bridge that’s said to be the first of its kind: Phoenix, a circular, 3D printed concrete masonry bridge that stands through compression without reinforcement. The bridge, located at Holcim’s Innovation Hub in Europe, was built using its proprietary ECOCycle circular technology and a custom concrete ink with 10 tons of recycled materials inside. Holcim partnered with the Block Research Group at ETH Zurich, Zaha Hadid Architects Computation and Design Group, and incremental3D to create the bridge, which demonstrates how combining circular construction and 3D concrete printing can enable low-carbon infrastructure applications. As Holcim explained, “Phoenix resulted from the partial recycling of aggregates” from the original blocks of 3D concrete printed bridge Striatus, launched by these same partners during the 2021 Venice Biennale of Architecture.
“I am thrilled to unveil Phoenix, a monument to sustainability and the result of a fruitful collaboration with our partners to meet a common goal: demonstrating that essential infrastructure can be designed and built in a way that is circular and lowcarbon today,” stated Edelio Bermejo, Head of Global R&D, Holcim. “This project showcases the impact that innovation can have in Holcim’s mission to decarbonize building for a net-zero future.”
OZRUH Launches Furniture Collection Made with 3D Printed Sand
London-based architectural design firm OZRUH, founded in 2019, creates designs that are novel and intelligent and, as it states on the website, “made by the principles of divergent evolution, advanced computational processes, and innovative manufacturing techniques.” Its latest furniture collection definitely fits—each piece in PRIMITIVES [1] is 3D printed using recyclable quartz sand particles. Each sculptural, detailed nightstand in the collection shows the firm’s exploration of creating voxel-based shell geometries by controlling erosion. The method used to print the pieces is based on binder jetting, and the collection marries innovative aesthetics and sustainability. Quartz sand, which can be recycled several times, is the main material, and a dissolvable material binds the sand without the use of high temperatures, which improves production efficiency and supports sustainability.
“The goal is to make designs that blur the contrast between archaeological and geological forms to aim for greater longevity than typical modernist geometries. Allowing the pieces to be more receptive to adapting to unexpected conditions, external pressures, and erosion. This range of sculptural furniture demonstrates how we can use 3D printing methods to push formal experimentation and novelty with new applications of ancient materials to create long-lasting functional art,” said Levent Ozruh.
“Our studio believes that embracing the idea of antifragility* in architectural design offers a great opportunity to discover new ways to create shapes and structures while also making designs more sustainable. This way of thinking is similar to how we see natural materials like rocks as complete, even if they have some irregularities – differentiating from modern design, where even a small chip on a cube’s corner is seen as damage.”
Made Plus Inc Using ETEC Xtreme 8K for Planet-Positive Footwear
U.S.-based footwear company Made Plus Inc. (made+), a Desktop Metal customer, is pioneering planet-positive manufacturing, and using the ETEC Xtreme 8K DLP 3D printer to make shoes. In addition to 3D printing, the company uses machine knitting and digital modeling in its on-demand manufacturing model. Customers can visit the all-in-one product customization platform to choose from hundreds of color combinations for their shoes, which offer a choice of either a conventional polyurethane cushioning system or an exclusive 3D printed lattice insole. Each pair in the company’s debut shoe collection, the Skiff, is made in Maryland, incorporates azo-free dyes, and has a stylish, contemporary design. Follow made+ on Instagram to get 10% off your next custom order with the promo code M+instagram.
“Our innovative approach to making shoes not only ensures quality, fit and performance but also aligns with a responsible, environmentally conscious lifestyle,” the company states on its website.
“By choosing made+ footwear, you’re making a conscious decision that positively impacts our planet without sacrificing look and feel.”
Snapform & Create it Real 3D Printing Prosthetic Sockets with FDM
Prosthetic clinic Snapform, based at the Technical University of Denmark (DTU), is dedicated to improving the lives of amputees by reimagining how to make affordable, custom-fitted prosthetics with the latest digital technology, including its prosthetic fitting engine SimFit. Recently, the company was excited to share that it’s made positive progress in exploring the potential of Fused Deposition Modeling (FDM) as a way to make prosthetic sockets. This method is usually thought to be not strong enough for prosthetics, and many prefer to use Selective Laser Sintering (SLS) instead. This work came about through a collaboration with fellow Danish company Create it REAL to investigate and test the capabilities of FDM printing for prosthetic sockets. Snapform conducted a strength test on an FDM printed socket made by Create it REAL, and announced in a LinkedIn post that “it passed the maximum strength test according to ISO 10328.”
“The potential impact of this achievement is enormous. With Snapforms Simfit program combined with Creat It Real’s printing technology, there’s a significant opportunity to dramatically reduce the cost of prosthetics. This breakthrough opens doors for countless amputees worldwide who currently lack access to high-quality prosthetics.”
Subscribe to Our Email Newsletter
Stay up-to-date on all the latest news from the 3D printing industry and receive information and offers from third party vendors.