Listen to this article |
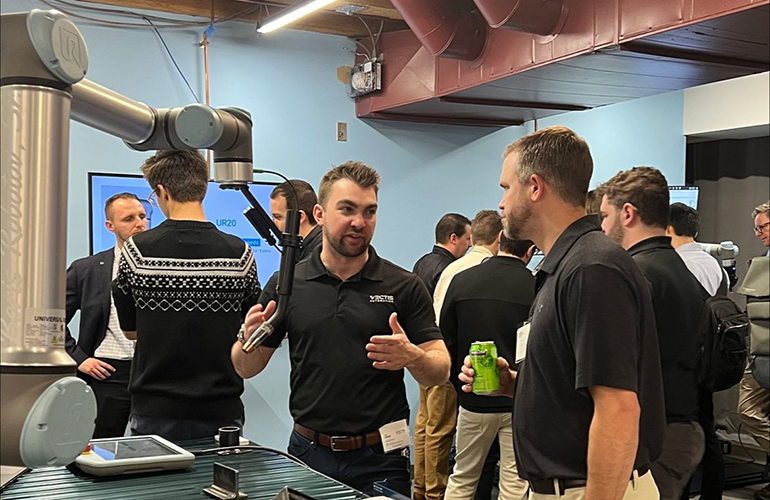
Universal Robots partners discussed and showed cobot applications at its Boston open house. Source: Universal Robots
BOSTON — Once dismissed as not capable enough for industrial use, collaborative robots are just beginning to help manufacturers and supply chains. At an open house at its U.S. headquarters yesterday, Universal Robots A/S showed about 400 attendees that cobots are ready for production work at shops of all sizes.
Collaborative robots are smaller and lighter than some industrial robot arms, and they include sensors, software, and other features to make them easier to program and to work alongside people. In the past few years, they have become more powerful, more precise, and even easier to use, noted Universal Robots.
The unit of North Reading, Mass.-based Teradyne Inc. demonstrated several cobot applications with select partners during its open house. Each one combined a UR arm with sensors such as those from SICK, end effectors from OnRobot and Schunk, and Universal Robots’ own controllers. Unlike typical industrial robot workcells, the exhibits didn’t require safety cages.
Universal Robots also offered presentations throughout the day, discussing topics ranging from a customer use case and risk assessments to the future of work. Here are five takeaways from the event:
1. Collaborative robots are ready for palletizing
Putting boxes or cases on pallets can be strenuous, repetitive work. Larger cobot arms, advances in motion control, and Universal Robots’ focus on applications rather than technology for its own sake led to a veritable explosion of automated palletizing demos at this year’s trade shows, such as Automate, ProMat, and PACK EXPO.
Robotiq showed its Robotiq Palletizer, which included a UR10 arm. Ryan Weaver, vice president, commercial, discussed how “lean robotics” best practices can help companies get started with automation.
“We had talked a lot about lean robotics before the [COVID-19] pandemic, but now it’s time to help companies with adopting robots,” he told The Robot Report.
On display was the UR20 model, which is now shipping. It can handle payloads of 20 kg (44 lb.), making it suitable for palletizing, welding, and other tasks once the province of industrial robots.
Other Universal Robots partners around palletizing included systems integrator Flex Line, with its boxEZ Box Erector.
Mobile Industrial Robots, which is also owned by Teradyne, showed its MiR 250 autonomous mobile robot (AMR). Brian Dillman, sales director at Odense, Denmark-based Mobile Industrial Robots, talked about how logistics can go “from good to great using AMRs.”
Many AMR users have gone from “kicking the tires” to wanting to scale their robot fleets within and across facilities, Dillman said. He offered guidance on how to manage such growing fleets.
2. Cobots offer flexibility for machine tending
The right combination of machine vision, software, and UR cobots can facilitate CNC machine tending. However, implementation can be a challenge, observed Tyler Bouchard, co-founder and CEO of Flexxbotics.
Flexxbotics provides support for cobot machine tending, and the company claimed that its FlexxCORE software connects robots with other equipment for tasks such as deburring. With an edge box and cloud-based platform, it’s easy to apply programming across cells, noted a Flexxbotics representative at the open house.
Precision Cobotics, another Universal Robots partner, demonstrated its laser marker for picking operations.
3. Universal Robots continues to grow its ecosystem
“We originally expected only 200 people,” said Zach Tomkinson, regional manager for East U.S. sales at Universal Robots.
Attendees came from as far away as Georgia and North Carolina for the one-day event. They included a mix of potential end users, integrators, engineers, startups, and students, as well as organizations such as MassRobotics. Several told The Robot Report during networking that they were looking for solutions to common industry challenges.
While Universal Robots has specialized in collaborative robot arms, it said its growing UR+ partner ecosystem enables users to find the right mix of already-compatible technologies for their needs.
For instance, Kane Robotics displayed its GRIT-ST system for precision surface finishing, and ESTIC America demonstrated an automated nut runner for assembly. New Scale Robotics showed its Q-Span system with a UR cobot for automated gauging.
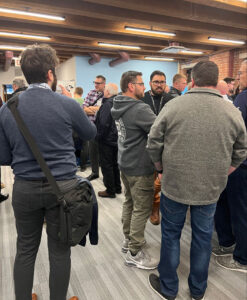
More than 400 people attended UR’s open house. Source: Universal Robots
4. Automation is becoming accessible to shops of all sizes
Force-torque sensors provide a sense of touch, and increasing integration of vision systems is allowing robots to keep picking autonomously rather than give up after a single try, explained Andrew Pether, principal innovation research engineer at Universal Robots.
In combination with demonstration learning and streamlined user interfaces, shops that don’t have robotics expertise can now adopt automation, he said.
Vermont Creamery explained how it journeyed from “evaluation to FAT” (factory acceptance test) as a UR customer. Rick Bart, director of operations; Chris Freeman, operations manager; and Eric Duncan, supervisor for environmental health and safety, provided the end-user perspective on a successful deployment.
Vectis Automation showed its Cobot Welding Tool for fabrication shops, and Cobot Systems displayed its Laser Welder. Hirebotics also offers integrated welding automation including UR cobots.
In addition to its open house, Universal Robots hosted training sessions at its headquarters as part of its “UR Academy.”
5. Don’t fear robots and AI — they’re here to help
Despite widespread reports warning of job losses as a result of robotics adoption, such a correlation hasn’t been proven, said Julie Shah. She is a professor at the Massachusetts Institute of Technology’s Computer Science and Artificial Intelligence Lab (MIT CSAIL).
“Our lab prefers to focus on ‘positive-sum automation’ rather than a ‘zero-sum’ stalemate,” she said in a session on the future of work. Shah said her research is working on computing at augments human capability.
In addition, small and midsize firms represent 48% of U.S. manufacturing and employ 43% of manufacturing workers, Shah added. If only one-tenth of automotive suppliers are using robots and all complain of a dearth of skilled workers, automation is part of the solution of upskilling labor, she said.
Shah divided industrial automation into three phases. From 1962 to about 2010 was the “Don’t go there” stage, with heavy robots caged away from human workers.
2011 to 2021 was the “Get out of the way” phase, with cobots and collaborative mobile robots learning to move or stop around people, according to Shah.
On a related topic, Chris Savoia, head of strategic business development at Universal Robots, covered how and why to conduct risk assessments for cobots in a separate session. Collaborative robots are designed to be safer to operate around humans, but users must still take workspaces, payloads, and processes into account, he said. Fortunately, there are best practices and standards to help, Savoia said.
From 2022 into the future could be the era of “positive sum automation,” said Shah, as robotics developers overcome challenges such as when a robot freezes completely in proximity to a human co-worker.
Light curtains, a range of sensors and software, and artificial intelligence to predict human motion can all help robots become more aware, she said. Such predictive abilities, along with more accurate simulation and measurement, can lead to better integration and test, Shah said.
While it’s still early days for generative AI and human-machine interaction, Shah said the best productivity results are likely not from “lights-out,” fully automated factories but from smart collaboration between humans and robots.