Researchers at the National Center for Supercomputing Applications (NCSA) and The Grainger College of Engineering, University of Illinois Urbana-Champaign (UIUC), have made strides in stress prediction research using artificial intelligence. Their work, focusing on deep operator network (DeepONet) implementations, aims to improve stress response predictions in complex geometries, such as those found in additive manufacturing. Utilizing the NCSA’s Delta system, they’ve achieved significantly faster results compared to traditional finite element methods.
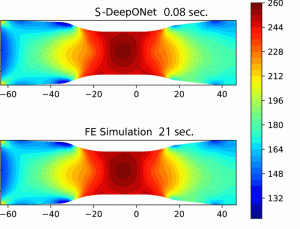
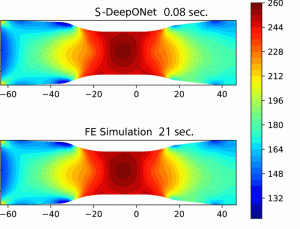
The team conducted their research through Illinois Computes, a program offering extensive computing and data storage resources. This initiative has facilitated collaboration across various disciplines, combining machine learning and computational mechanics. The Delta system, renowned for its high-performance GPU computing capabilities, was crucial in training deep neural networks and generating training data using Abaqus software.
Two significant publications have emerged from this research. The first, in “Computer Methods in Applied Mechanics and Engineering,” introduces a novel DeepONet using a residual U-Net (ResUNet) for encoding complex geometries. This approach marks the first use of ResUNet in DeepONet architecture, demonstrating superior memory efficiency and flexibility over traditional methods.
The second paper, published in “Engineering Applications of Artificial Intelligence,” describes another innovative DeepONet version, S-DeepONet. It leverages advanced sequential learning methods, offering enhanced accuracy in multi-physics solutions under varying thermal and mechanical loads.
“Additive manufacturing is a revolutionary manufacturing technique that opens nearly unlimited possibilities for its implementation,” said said Iwona Jasiuk, professor of mechanical science and engineering at UIUC..
“DeepONet serves as a powerful and rapid computational tool, which can simulate the additive manufacturing process at various spatial and temporal scales. Such simulations are needed for deeper understanding of the additive manufacturing process and its implementation and monitoring.”
This research is not just a leap in AI applications but also holds significant implications for advanced manufacturing processes and the development of digital twins. The collaborative effort between NCSA and MechSE highlights the synergy of multidisciplinary expertise and cutting-edge technology.
Come and let us know your thoughts on our Facebook, X, and LinkedIn pages, and don’t forget to sign up for our weekly additive manufacturing newsletter to get all the latest stories delivered right to your inbox.