The week after Thanksgiving, the Biden administration provided the world with major insight into what will be driving the White House’s activities in 2024 (beyond Biden’s campaign for reelection). The administration announced the establishment of a Council on Supply Chain Resilience, which is co-chaired by the National Security Advisor and National Economic Advisor, and includes essentially all cabinet-level agency heads.
This obviously has the potential to mark a major turning point in the advanced manufacturing landscape of the U.S., with particular ramifications for the additive manufacturing (AM) sector, given its comparative edge in technological maturity over other areas of Industry 4.0. Ultimately, AM’s opportunity to embed itself into the next generation of industrial policy may only be limited by the viable use-case examples that companies within the sector can devise, recommend, and around which they can partner with each other — and with the government — to implement.
Along these lines, industry professionals should start getting proactive about developing practical, broad-based solutions for deploying AM across whole enterprises. One of the best places to start may not even be by focusing on the printers themselves, or even the necessary material inputs, but on optimizing the ability to identify, record, and evaluate viable part candidates to be 3D printed.
This may all start with 3D scanners. Sergey Sukhovey, chief experience officer and a co-founder of one of the world’s leading 3D scanner brands, Artec 3D, shed some light for me on how a company’s 3D scanning capabilities can greatly enhance the resilience of its supply chains.
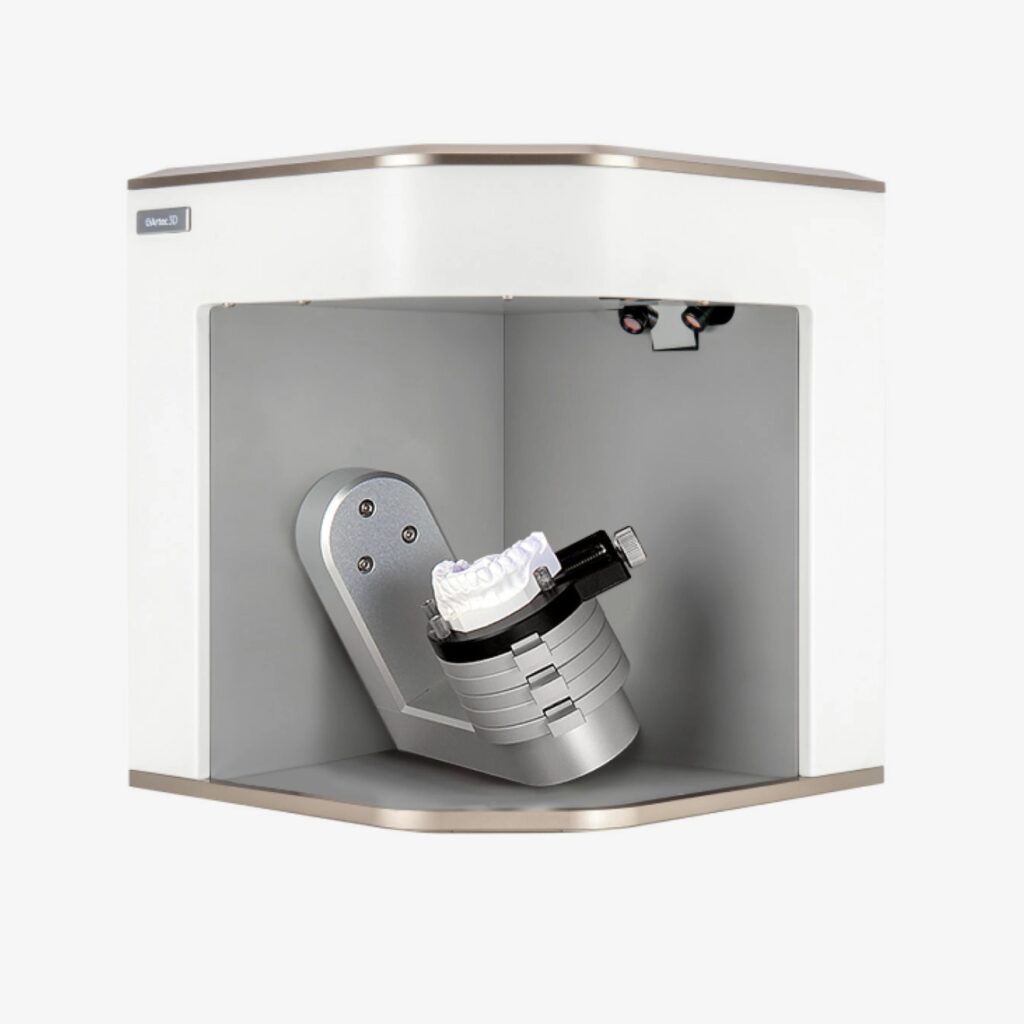
Artec 3D has lived the experience of supply chain resilience firsthand, having started to relocate a portion of its operations the very first week of the Ukraine invasion. Although this was just Artec 3D’s R&D branch — all of the company’s production takes place in Luxembourg and the U.S. — it nonetheless gave the company direct insight into the exact dynamics at-hand in the current era where disruptions are routine.
Artec 3D scanners are also widely used by the U.S. Department of Defense (DoD). AST2, one of Artec 3D’s authorized resellers, notes on its website, “Our principal customers are Department of Defense agencies, and our customers use Artec scanners for innovation, rapid prototyping and reverse engineering (RE) to support national defense requirements.”
Given the DoD’s central role in catalyzing and structuring the U.S. government’s push to build up domestic advanced manufacturing capabilities towards the goal of supply chain resilience, organizational compatibility with Artec 3D could fast-track AM companies’ plans to benefit from, and benefit to, the emerging industrial policy landscape:
“Industries can use 3D scanners to streamline the reverse-engineering manufacturing process and improve quality inspection for faster and more accurate methods of ensuring products meet standards at every stage, further speeding up production lines,” Sukhovey explained. “By using 3D scanners, there is a decrease in the human factor, minimizing errors that would undoubtedly be present when measuring by hand. Also, once the original 3D data is captured and saved it can be checked and verified by other people and teams. This increases efficiency and allows various team members to always have the source data available to return to. Having access to such data also allows the expertise to be split between different people.
“Another way 3D scanning can support the supply chain is by monitoring and tracking shipments to prevent loss and damage. This can be done by both scanning exports to check for quantity and for checking defects in products at various points of manufacturing and shipping.”
It is built into the concept of creating digital repositories, that staying proactive is the best way for a company or organization to keep its supply chains resilient. As is becoming more and more apparent from observations of all major areas of advanced manufacturing, the factor that advanced manufacturing enterprises may need to be the most proactive about is workforce development. 3D scanning is an almost ideal skillset for those in the world of advanced manufacturing to start building their workforce development strategies around:
“Training teams to use 3D handheld scanners requires very little training, and once personnel are trained, it reduces labor hours. In geographical areas that are difficult to access, this means faster repair cycles when using 3D scanners in combination with 3D printing. For example, on ships that have 3D printers installed, quick checks and repairs can be done on-site, without the need to return to and spend time in docks. Companies can also include 3D scanning in their risk analysis and maintenance plan to make sure they are constantly and consistently measuring quality, and are able to address problems as soon as they appear, avoiding larger problems further down the line.”
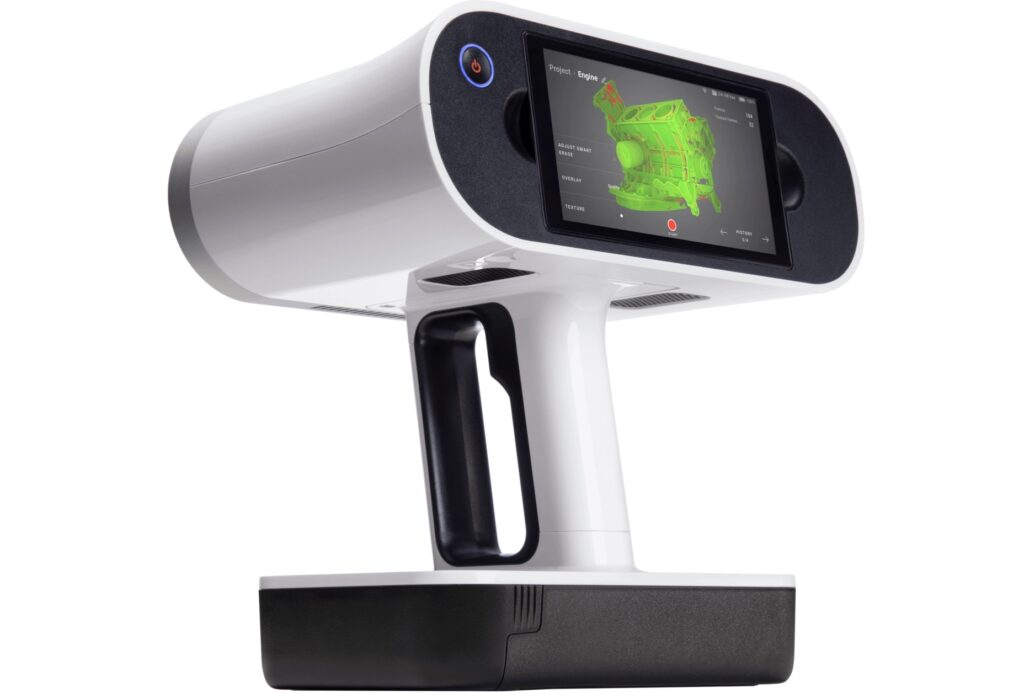
Sukhovey also made the crucial point that, while global attention only started to turn towards supply chain difficulties after the onset of the pandemic, those difficulties were in fact present well before anyone knew what COVID was. The effect of the pandemic, Sukhovey explained, was to exacerbate all of those already existing tensions, bringing them to the surface:
“Disruptions were not seen for everybody, but for many they were present and demanded essential changes even before COVID. For example, in the past, producers of microelectronics generally kept products on the shelf for a much longer time before discontinuing products, which allowed manufacturers to make purchasing decisions with less immediate notice. Already leading up to COVID, however, changing financial habits started to steer towards reduced lead time before products became discontinued, with the expectation being that the purchasers should simply adapt quickly to those changes. Resultantly, there has been an increased need to stock up on essential components well in advance, in order for enterprises to avoid the disruptions to their supply chains that come with increased lead times for delivery of parts.
“And, post-COVID, the already long lead times have become even longer. Additionally, we can see a shift from dependence solely on imports from abroad, and nations’ greater recognition of the need for autonomy in their manufacturing bases. In the US, of course, the focus involves reducing dependence on imports from China and increasing capacity to manufacture domestically — not just for products to be sold in the US, but for exporting to other countries, as well. In general, there is an increased need to identify the most important components a company depends on, and to find ways to secure supply of those parts so that they’re resilient to unexpected risks and threats.”
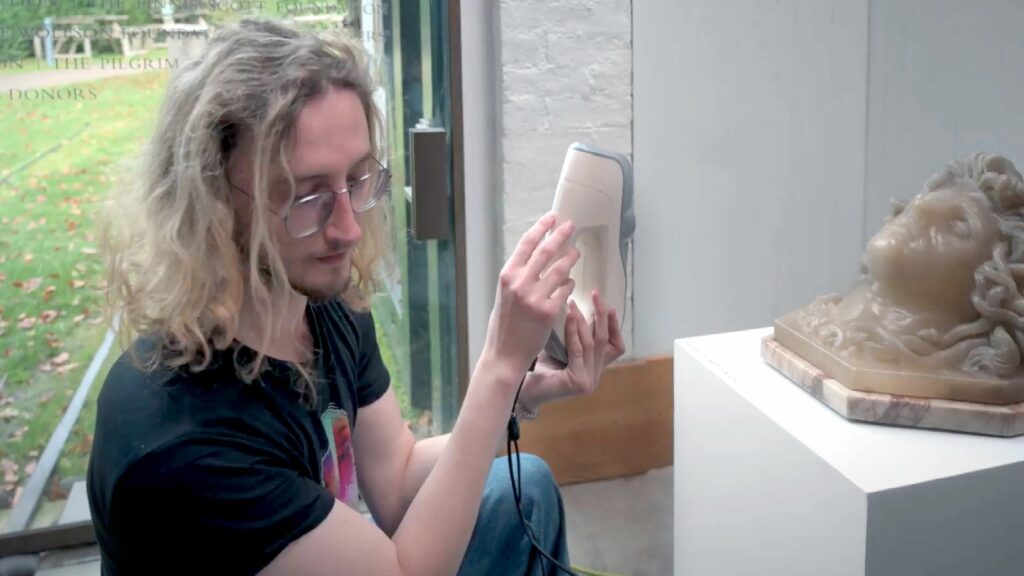
This sums up why, even as disruptions resulting from the pandemic and Russia’s invasion of Ukraine have started to subside somewhat, the White House has only just begun to ramp up U.S. efforts to reshore the industrial base. As much as global supply chains have been thrown into disarray by the major events thus far in the first half of the 2020s, these initial challenges seem like mere precursors to much more fundamental shifts ahead.
Unsurprisingly, then, the precedents set by the U.S. and China to shore up their domestic advanced manufacturing capabilities are mirrored in all of the other most highly industrialized nations around the world. As the institutional transformations begin to set in, don’t be surprised if the already sizable financial backing behind those changes escalates much further:
As Sukhovey simply put it, “Financial support always helps. The production of chips, to name one example, is nothing if not capital-intensive, so government support of businesses that can bring manufacture of high-tech industrial parts into the domestic economy is key. Thus, even aside from direct support, ensuring the existence of adequate local infrastructure is another way governments can help. For example, the Luxembourg government has invested heavily in a huge data center — a large facility with ample processing power and storage which enables and encourages tech companies to operate and thrive.
In turn, networking is always a great way for companies to put themselves in the best position to succeed. At Artec 3D’s opening of a new production facility earlier this year, former Luxembourg Prime Minster Havier Bettel and Minister of Economy Franz Fayot both attended. This encouraged the success of the opening, and their presence demonstrated a significant endorsement of the company and the new facility, which greatly helps to draw awareness to the cause.”
A whole new era of industrial policy has emerged, and we are just beginning to understand the implications. Grasping the nature of the change is overwhelming, but as Artec 3D illustrates, now is always the best time to start thinking about how to approach the future.
Images courtesy of Artec 3D
Subscribe to Our Email Newsletter
Stay up-to-date on all the latest news from the 3D printing industry and receive information and offers from third party vendors.