Back in June, the US Navy announced that additive manufacturing (AM) specialists at the Southeast Regional Maintenance Center (SERMC) in Mayport, Florida had invented a new tool for the MK 15 Phalanx Close-in Weapon System (CIWS). AM Coordinator Chief Machinistâs Mate, Nicholas Heinrich, worked with civilian CIWS Technician, Terry Henderson, to 3D print an aluminum device used for replacing motors on the CIWS.
Now, the SERMC has announced the use of 3D printing for a replacement part â the original was made with injection molding â on the USS Farragut (DDG-99). Maintenance on the Farragut at SERMC was almost done when lieutenant junior grade (LTJG) Anton Tyree, USS Farragut Electronics Material Officer, and other personnel on the ship spotted a malfunctioning part on the shipâs radar system.
Heinrich reverse-engineered the injection molded part âin about 40 minutesâ, and within a few hours of that, the new part was printed. Heinrich printed an additional part as well, to equip the Farragut with a spare while itâs at sea. The new part has now been in-service for several weeks without issue.

Regarding the new 3D printed part for the USS Farragutâs radar system, Heinrich said, ââŠthe 3D printed version was made with more rigidity than the original [injection molded part]. If any ship on the waterfront needs the same part, we can manufacture a new one in about two hours.â
SERMCâs commanding officer, Captain Justin Dowd, said, âThis accomplishment is another historical first for our 3D Lab here. Today we demonstrated that if a customer on the waterfront needs something quickly, they can rely on SERMCâs talented workforce and new printers to deliver a high-quality solution to the warfighter in a short period of time.â
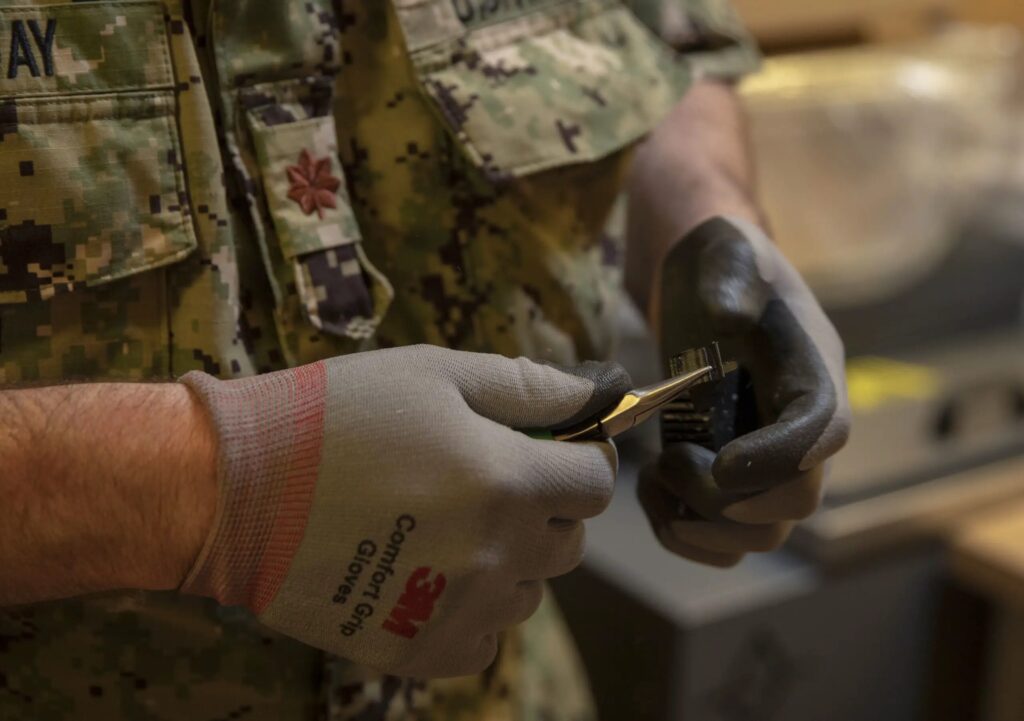
It is important to stand back and recognize the many different elements comprising developments like this one, as well as the earlier development with the CIWS:
- A US Navy vessel was able to complete its maintenance on time, in a scenario where that may not have otherwise been the case
- A new part was designed and produced within a matter of hours, providing everyone involved with a successful workforce experience surrounding 3D printing
- The new part was not only able to be designed and produced right at the point of need, but also may prove to outperform the injection molded part it replaced
All three of these advantages were able to be delivered simultaneously because of AM.
Thus, while there are certainly headwinds being faced by the AM sector at-large, there is also, simultaneously, a huge success story bubbling under the surface, embodying all the features of the long-term vision for AMâs potential. Moreover, the main character of that success story is the quintessential early adopter of new technologies, the US military.
The buildup to this has been years in the making, and it is truly just the beginning, as is detailed in the report that Tali Rosman and I co-wrote, published last month, âAdditive Manufacturing for Military and Defenseâ. No one knows precisely what the AM sector will look like in 2024, but one thing that is certain is that the US military will continue ramping up its AM use-cases, driving the technology towards greater maturity at an even faster rate. When the military discovers something that it likes, its tendency is to keep doubling down in the same direction.
Subscribe to Our Email Newsletter
Stay up-to-date on all the latest news from the 3D printing industry and receive information and offers from third party vendors.